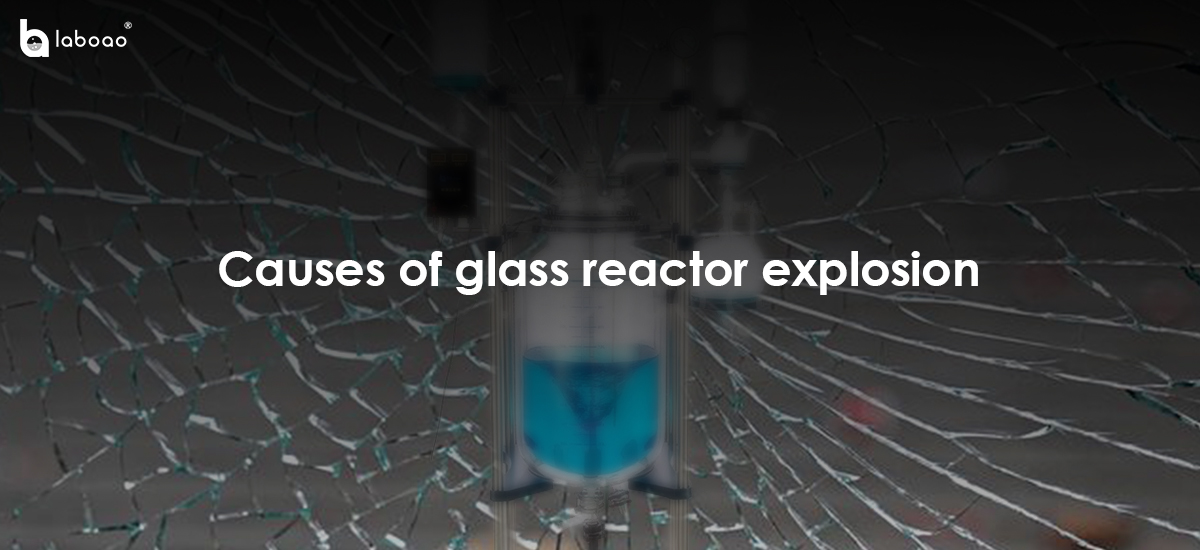
First of all, in the working process of the double-layer glass reactor, some places are actually easily overlooked by users. Once the double-layer glass reactor explodes, it will be very dangerous and threaten people's lives and property in production tests. It is of utmost importance to grasp the causes of the explosion of the double-layer glass reactor and effectively curb the occurrence of this phenomenon.
1. The violent reaction of the substance will cause the reactor to explode. Some chemical reactions are exothermic reactions. When the reaction temperature exceeds the specified temperature, the material produces a large amount of gas, which causes the pressure in the kettle to increase sharply. Causes large-scale explosions in the enterprise.
Solution: Pay attention to control and timely record the changes in the reaction temperature of the material during operation to prevent the temperature from being too high and causing violent reactions:
2. Install a pressure relief device to automatically reduce pressure when the pressure in the kettle increases. Another situation is that when two materials come into contact, a large amount of reaction heat is generated. When the material is close to the kettle wall, the heat release forms a drastic change, causing multiple point-like explosions. Jacket overpressure will cause the reactor to burst. When chemical companies use steam output from power plants to provide heat for production, the steam output from the power plant can only be used after decompression. Once the pressure reducing valve fails, or the steam buffer tank safety valve fails, the high-pressure steam output by the power plant is directly input into the double-layer glass reactor jacket, forming an overpressure of the jacket, and the kettle wall bulges due to external pressure to form a large-scale burst.
Solution: Install another pressure reducing valve on the basis of the existing pressure reducing device, and change the first-level pressure reducing to the second-level pressure reducing to achieve double insurance. In addition, the working condition of the pressure reducing valve should be checked frequently, and the problem should be replaced immediately. Some should check whether the steam safety valve is in the correct working state, especially the spring safety valve to keep it working in a clean environment, and no corrosion or jamming should occur.
In addition, during the operation of the double-layer glass reactor, we should also pay attention to the following aspects:
1. Pay attention to insulation. Since the thickness of the interlayer in the middle of the double-layer glass reactor is small, the insulation performance is poor. In the process of using high and low temperatures, users need to use insulation materials to insulate the kettle body. At the same time, users need to wrap the reactor body and the pipes for the circulation of heat-conducting medium with insulation materials, and pay attention to the thickness of the insulation layer to ensure a good insulation effect.
2. Selection of temperature control medium. For general enterprises, users will choose temperature control media of different social properties as a heat transfer medium for a reaction according to the required reaction temperature. Choose ice ethanol for low temperature, water for room temperature, and dimethyl silicone oil for high temperature. The industry recommends that when using low or high temperature, pay attention to choosing the right medium, the key lies in viscosity. If the viscosity of the medium is too high, the circulation pump may not move, the medium circulation effect is not good, and the required temperature control effect cannot be achieved. When replacing a high-power circulation pump, the pressure of the medium is too large, which is easy to damage the double-layer glass reactor lining and cause the reactor to rupture.